Technologies like Machine Learning [ML], Artificial Intelligence [AI], Cognitive Computing, Robotics, Cloud Computing, Internet of Things [IoT], and more are transforming each & every sector in business. The traditional manufacturing industry is also at the cusp of a major revolution and these technologies & processes are the key enablers of the disruption.

Industry 4.0 [I 4.0], also termed the fourth industrial revolution is a transformation that makes it possible to analyze & gather data across machines and improve processes resulting in better productivity at reduced costs. Autonomous robots, Collaborative Robots [Co-bots], Industrial Internet of Things [IIoT] and Additive manufacturing are termed of the key building blocks of I4.0 [Source].
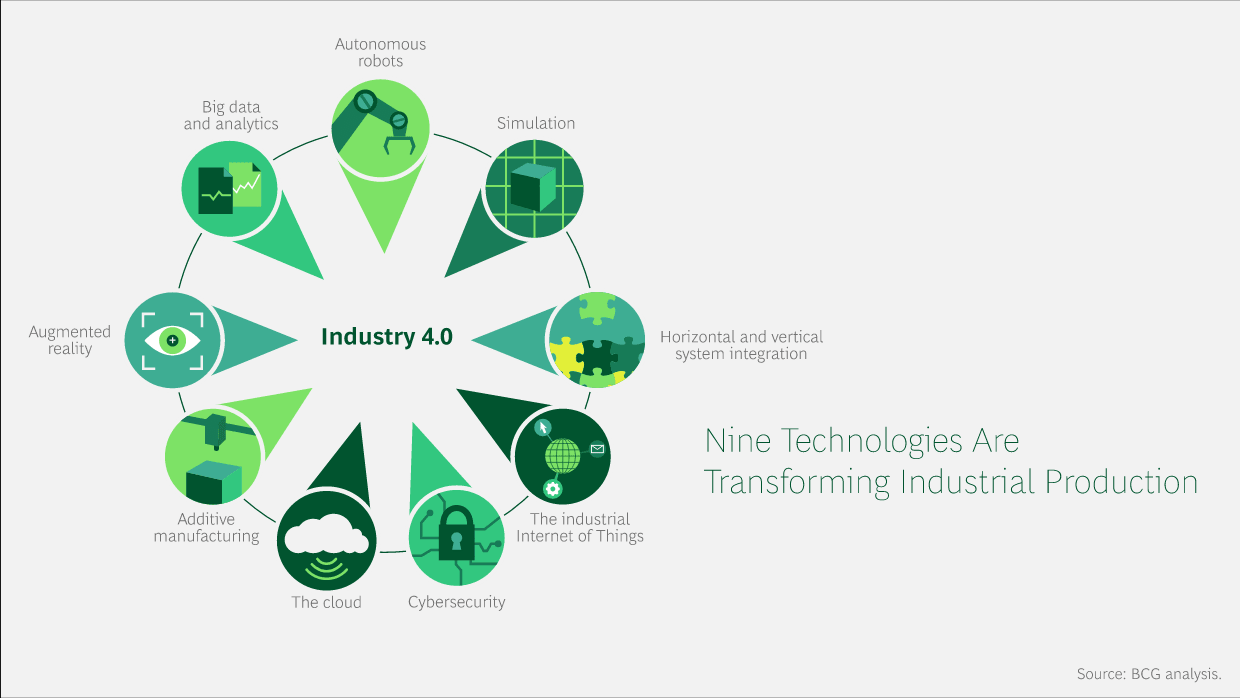
In the Indian market, 20 billion devices are set to be connected to IoT by 2021. The adoption of IoT and IIoT will span across different industries like manufacturing, retail, supply chain, automobiles, healthcare, etc. I4.0 is the future of automation & smart factories and these are some of the technological trends in 2020 that will enable Indian industries to march towards the fourth industrial revolution.
Talking about smart manufacturing processes, Wienerberger is one such company that proved to be a leader in producing clay-based building materials – wall, roof, facade solutions. It is the world’s No.1 brick manufacturer. The company is constantly engaged in leveraging technology and innovation to provide world-class building material solutions. Under the brand name Porotherm Smart Bricks, Wienerberger India has been manufacturing perforated Clay Blocks that are designed to provide improved durability, ease of use, and many other benefits that aid in cost-effective wall construction [Source].
Heavy Duty automation and the use of technology has made Wienerberger, by far, one of the largest clay block producers in South East Asia. With hi-tech robotics aiding the production process of over 70,000 large format blocks which is equivalent to 630,000 regular bricks per day, it is evident that the need for electricity is very substantial. 95% of the factory requirement is met through renewable energy including solar and wind. To cut down on emission the factory converts fossil fuel to a sustainable energy source, that is converting coal to natural gas as a fuel.
We were invited to Wienerberger’s Kunigal factory that is located in the Tumkur district of Karnataka in November 2019. Due to a busy schedule, we could not come up with a timely post on the same. Better late than ever!
Wienerberger AG, announced an investment of Rs. 30 crore in their Kunigal factory and the announcement was made by Christof Domenig, CEO, Wienerberger Building Solutions. The announcement was made on the company’s 200th anniversary and 10th anniversary of operating in India at Wienerberger’s factory in Kunigal.
The investment will enable the company to support its expansion plans including an upgrade and an implementation of new equipment in the factory, converting to natural gas as a fuel and launch of new building solutions that will enable construction practices to be simplified and faster with less resource consumption.
Wienerberger launched its first operation in 2009 in India wherein the company started production of its Porotherm smart clay bricks out of its Kunigal factory. Since its operation in India, the company has built more than 45,000+ apartments across South India and 15,000 independent houses in addition to building many other prominent and prestigious hospitality and educational institutions.
Myself, along with fellow bloggers and journalists had an opportunity to take an insider’s look in their manufacturing facility that uses state-of-the-art technology like Robotics and has extremely energy-efficient manufacturing processes. The impressive part about the factory tour was that the entire factory is managed by less than 20 people and robots were engaged for material handling.
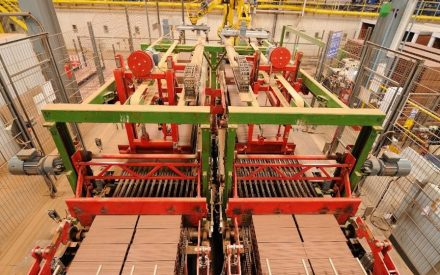
The unit uses sustainable practices in manufacturing through the usage of natural additives like granite waste, rice husk, sawdust, and coal ash as inputs. Totally 30,000 units of power is consumed on a daily basis, out of which 95 percent comes from solar energy [Source]. The representatives of Wienerberger also shared their valuable insights on smart manufacturing and I4.0. More details about the Wienerberger’s India factory can be found here.
So far the company has managed to channel over 92% of its electricity needs is used from solar and wind energy. This has helped Wienerberger India to successfully set benchmarks for the building manufacturing industry across the country and the world at large.
To mention a few of the high-end automated machinery used in the factory are:
The factory is also highly equipped with a full-fledged in-house laboratory and product development facilities. Currently, Wienerberger employs about 250 employees in India. The company is also strongly associated with several CSR activities like providing primary healthcare facilities and affordable housing in the vicinity of the factory.
Christof Domenig, CEO, Clay Building Materials Europe, Wienerberger AG, said
The investment in our Kunigal factory operations will include converting from solid fuel to a cleaner and sustainable energy source – that is natural gas. When it comes to using electrical energy in the factory, 95 percent of the factory requirement is met through renewable energy sources of solar and wind.
Despite there being no such mandate, the measure to introduce natural gas as a fuel is a decision taken by Wienerberger proactively to ensure a drastic reduction in carbon emission, although it will incur additional cost for the company. Wienerberger is continuously striving to convert its production processes to low-emission energy sources.
Sharing his insights, Monnanda Appaiah, MD, Wienerberger India, added
With the Rs. 30 crore investment, we will also be upgrading our machinery and install new equipment with the latest technology that will enable us to scale up the production by up to 25%. The products manufactured in Kunigal offer significant technical advantages over conventional walling materials apart from being environmentally friendly and cost-effective.
We are also actively marketing and supplying clay roof and facade solutions across India and are also planning to expand the product portfolios for these offerings that would be extremely relevant for the Indian climatic conditions and consumer preferences.
Wienerberger’s India product portfolio currently includes clay building materials solutions for walls, roofs, and facades. Wall solutions include products like Porotherm HP, VP Load Bearing, Thermobrick, HP Grinded + Dryfix System; Roof Solutions include Koramic and Tondach, and Facade Solutions include Aspect.